November, 2014 – Masterblend International has completed a 3-month, $500K renovation of their water-soluble fertilizer blending room, equipment, and processes. The new system has proven to increase efficiency, purity, and accuracy of the blending process, while decreasing start to finish blending time by as much as 75%.
The new climate controlled blending room is equipped with state-of-the-art HVAC equipment optimized with monitoring systems to control temperature and relative humidity resulting in a drier product with maximum flowability.
New blending equipment utilizes a high-speed conveyor to transport raw materials to the blending system and into their final package in a fraction of the time of the previous system. The contained conveyor system is also simpler to clean and inhibits cross-contamination due to material build-up. The high speeds at which materials are transported in conjunction with the shorter route to the blending machine give the materials less time to segregate resulting in a more thoroughly combined final product.
“The new system allows us to provide a purer product with a longer shelf life to our customers,” says Mark Jeffries, Vice President at Masterblend International. “Our products have always been blended with the highest quality components, but the technologies involved in this new process optimize our product even further by dramatically reducing environmental exposure, blending more accurately and efficiently, and getting the product into its final packaging faster. These upgrades have made a great product even better.”
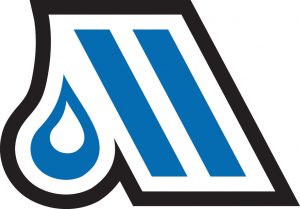